
RKS System Screen Printing Squeegees
The German precision made RKS squeegee blades...
The German precision made RKS squeegee blades are utilized in top screen printing operations worldwide as these quality conscious printers realize that exceptional standards for quality are paramount. They also know that you can’t become a world-class screen printing company without using RKS technology! Imitation is the sincerest form of flattery; There have been those whom have attempted to imitate (copy) the RKS precision squeegee blades but none can match their quality or consistency. The RKS factory in Rösrath Germany is state-of-the-art and they are ISO 9001 certified.
Introduction video to RKS high quality squeegees and machines
An RKS System Squeegee blade is built with two parts; first a hard-elastic carrier/ backing which provides a constant printing angle (18o is the RKS standard) and delivers uniform squeegee pressure and steady flexibility/ repeatability. The second component is a soft-elastic Vulcollan strip with provides an accurate "print edge" to provide perfect contact with the screen stencil. The RKS System Squeegee blade creates the perfect capillary action to transfer (push through) the proper amount of ink every stroke. Precision and Quality Control is what RKS is all about and the RKS System Squeegee blades give absolute parallel printing precision. Watch the video above and you will not see one single wavy printing streak which you know frequently occurs with a traditional squeegee blade.
The RKS System Squeegees are available in heights from 20 to 145 mm and have a Vulcollan strip thickness of either 6 or 8 mm (see charts herein). We can offer shore hardnesses from 55 to 80 durometer for a wide variety of screen printing applications. (Note the 55° shore material is only available in 8mm thickness). The two different Vulcollan material thicknesses provide a very fine grading of the hardening effect that the Vulcollan strips provide. For example, because of the fiberglass backer a 65 shore / 6 mm thick blade delivers a harder effect than a 65 shore / 8 mm blade.
RKS System Squeegees deliver repeatability & consistency:
RKS System Squeegees deliver the longest possible service life:
RKS System Squeegees are supplied with durometer ranges from 55 to 80 shore. RKS has managed to apply the latest technological advances to achieve the best possible physical strength characteristics and high resistance to inks & solvents, delivering optimal on-press performance. This means that the service life of an RKS System Squeegee blade reaches levels believed to be impossible up until this superior squeegee blade was developed.
It is a fact that RKS squeegee blades require less application pressure than a conventional rubber squeegee blades. This means that the screens and stencil image is subject to less wear & tear, leading to a noticeable increase in screen life and squeegee life. Less pressure equals less mechanical stress (deflection) for the entire screen printing machine.
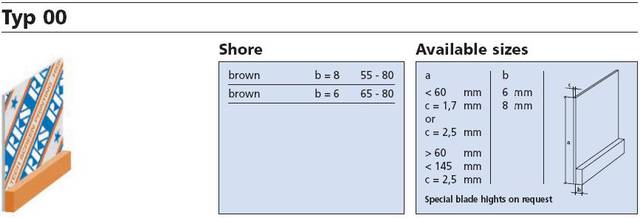
* Maximum production length approx 2800mm;
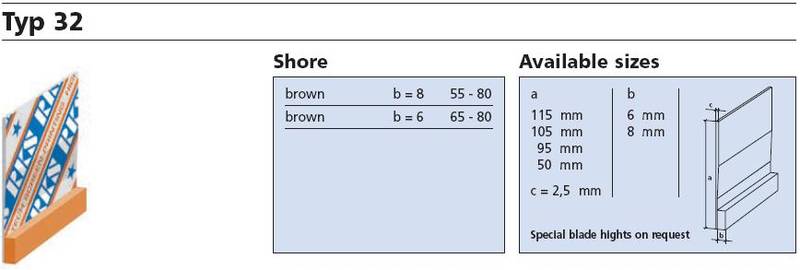
* Maximum production length approx 2800mm;
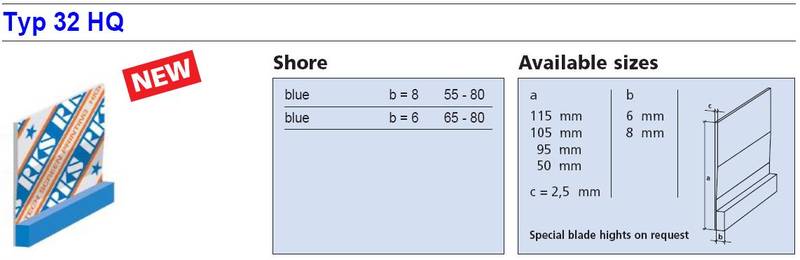
* Maximum production length approx 2600mm;
Traditional Squeegees VS. Exceptional RKS Squeegees:
If you are an experienced screen printing operator, then you know first-hand that traditional squeegee do not allow for consistency, repeatability & standardization of the screen printing processes.
The effects of solvents and other ink components change the squeegee materials permanently. The shore hardness of a polyurethane squeegee is reduced and causes the screen printing squeegee to lose its flexibility and this will change the attack angle (aka printing angle) and will directly affect the squeegee pressure. This makes it impossible to keep the initial set parameter of ink deposit and the image quality constant over a production run. With these variables, your screen printing results will remain an experimental process that needs constant attention by a highly skilled operator. To solve these problems (some may call them “nightmares”), the RKS company has developed the finest System Squeegee on the market… you need to try one to become an RKS believer! Ask us about our free sampling program to get you started.
Some Key Pointers or Recommendations:
1) For coarse or textured printing substrates / coarse fabrics / thick ink deposit we recommend using the 8 mm / 65 shore blades
2) For highly accurate/ fine detailed printing applications/ tight registration/ fine text sizes/ smooth surface finishes we recommend using the 6 mm / 75° shore blades
3) If you find that the flexibility of the RKS System Squeegee blade is too rigid for your specific screen print application, we recommend using the Carbon S squeegee blades as an alternative.
4) The optimum printing angle of an RKS squeegee is 18° (vertical plane is 0° in reference). To increase the ink deposit (laydown) the blade angle may be increased by 2° to a maximum of a 20° angle.
Function & Care of an RKS System Squeegee:
The RKS squeegee is a precision tool and as such, it must be handled properly. Compared with a traditional rubber squeegee, it requires less contact pressure for the same printing process, so start with minimal pressure and work your way up slowly until you get a quality print. Also ensure that the squeegee blade is parallel with the printed substrate, vacuum table or the impression cylinder (for roll to roll screen printing applications). If you change-out to a new RKS blade (of the same height), then you don’t need any adjustments or position corrections, you will get the same printing results! Never cycle the squeegee without ink in the screen as this will heat up the screen and blade material and the precision printing edge will break down or break off immediately. If that happens the you’ve got to stop production and head to the squeegee grinder and now your screen press is at a standstill. Also "non-stop printing" will cause damage to the service life of all polyurethane materials. Therefore we recommend that you change-out the squeegee after 5 to 6 hours when using solvent based inks and after 4 hours when UV cured inks.
So clean the RKS System Squeegee blade thoroughly after it comes off the press and let it “exhale” or relax for at least 12 - 24 hours before running that blade again. If you follow these guidelines your RKS System Squeegee will always work well and provide a constant tolerance range. Also by relaxing your blades there is no danger that the printing edge will break off, like it would if the blade was run too long and was swollen by the ink solvents or other volatile ink components. A little preventative maintenance goes a long way in increasing your blade life.