Pad Printing vs. Screen Printing: Processes, Applications, and Key Differences
The Differences Between Pad Printing and Screen Printing
Pad printing and screen printing are two versatile printing methods used widely across industries. Each method has unique strengths and applications, making them suitable for different projects. This article explores the key differences between these two printing techniques, including their processes, applications, and advantages.
1. Process Overview
Pad Printing
Pad printing, also known as tampography, is an indirect offset printing method. The process uses a silicone pad to transfer ink from an etched plate (cliché) onto a substrate. The pad’s flexibility allows it to conform to irregular surfaces, enabling printing on three-dimensional objects such as pens, golf balls, and medical devices. For an in-depth understanding, refer to this Introduction to Pad Printing.
Screen Printing
Screen printing involves pushing ink through a stencil (or screen) onto a substrate using a squeegee. While it is best known for printing on flat or slightly curved surfaces, screen printing can also be adapted for cylindrical or oval objects. Using specialized tooling such as rotary attachments or mandrels, screen printing can apply seamless designs to round containers (like bottles and jars) or oval containers (like cosmetic tubes). This versatility makes it a go-to method for industries requiring high-quality, full-wrap designs on packaging.
2. Substrates and Applications
Pad Printing
Pad printing excels in printing on complex shapes and surfaces. It is often used for:
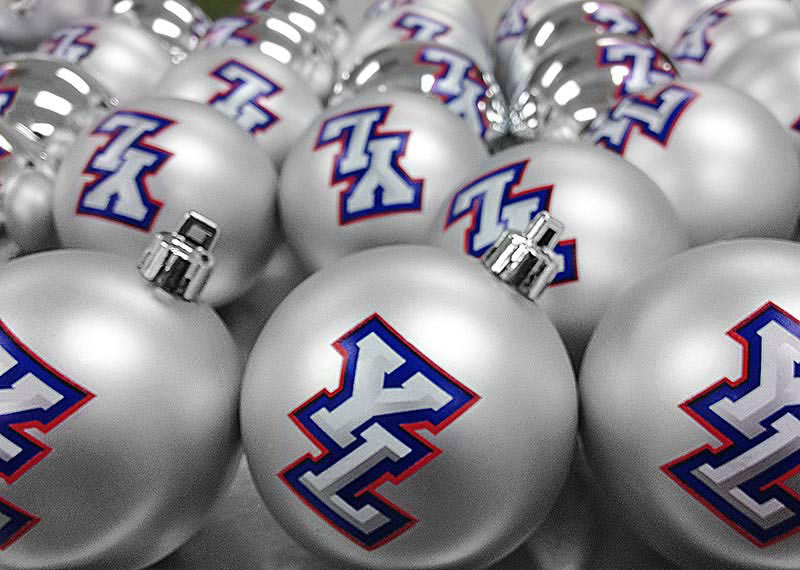
Example of pad printing on christmas ornaments, showcasing its ability to print on curved surfaces. (Source: Deco Tech Group)
- Consumer goods: Keyboards, computer bezels, mouse housings, and electronic components.
- Medical devices: Syringes, catheters, and similar surgical instruments.
- Automotive parts: Buttons, badges, steering wheel control keys, and other interior components.
- Toys: Minifigs, scale model cars, model train cars, and other similar objects.
- Sporting goods: Golf balls, baseballs, golf tees, club heads, etc.
Screen Printing
Screen printing is favored for applications requiring vibrant, rich-looking, and durable prints, such as:
- Containers: Plastic and glass bottles, cosmetic jars, aluminum water bottles, drinkware, and more.
- Textiles: T-shirts and apparel.
- Industrial applications: Circuit boards and solar panels.
- Signage: Posters, banners, display boards, and decals.
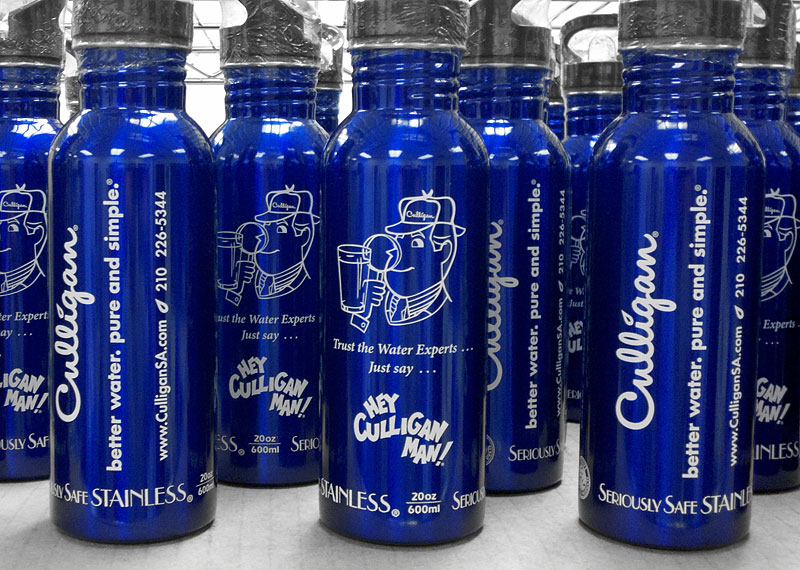
Screen printing example on cylindrical containers, offering bold, full-wrap designs. (Source: Deco Tech Group)
3. Ink Types and Coverage
Pad Printing
Pad printing inks are typically solvent-based to ensure quick drying and strong adhesion to various substrates, including plastics, metals, and ceramics. The ink layers in pad printing are thinner compared to screen printing, making it ideal for intricate and detailed designs but less suitable for applications requiring bold color or heavy solid ink layer coverage. Learn more about pad printing inks in this article on the advantages of pad printing.
Screen Printing
Screen printing primarily uses UV-curable inks due to their fast curing, durability, and vibrant finish. UV inks cure instantly when exposed to ultraviolet light, allowing for high-speed production and excellent adhesion to a wide range of materials, including glass, plastics, and metals. Additionally, the thicker ink layers achievable with screen printing make it ideal for bold, high-opacity applications that require long-lasting and visually striking results.
4. Production Volume and Speed
Pad Printing
Pad printing is versatile, offering options for semi-automatic and fully automated systems. Semi-automatic pad printing machines typically operate on a 3 to 5-second cycle, making them ideal for smaller production runs or intricate designs requiring manual adjustments. For higher-volume production, automated pad printing systems are used, capable of significantly increasing output while maintaining precision. Setup times for pad printing are relatively quick, generally 15 to 30 minutes. This combination of flexibility and efficiency makes pad printing well-suited for a variety of industries requiring high-quality and detailed prints.
Screen Printing
Screen printing on containers, especially with automatic UV screen printing equipment, is designed for high-speed production. These systems can achieve cycle speeds of less than 1 second per container, making them ideal for large-scale manufacturing. Automatic screen printers use UV-curable inks, which cure instantly, ensuring uninterrupted workflows and durable results. While setup for screen printing involves more extensive preparation—such as creating screens and stencils—the high-speed output and superior quality on cylindrical or oval containers make it highly efficient for large production runs.
5. Cost and Setup
Pad Printing
Pad printing offers cost-effective options for various production needs. The availability of long-run and short-run clichés helps manage costs for both high-volume and smaller production runs. Additionally, advancements such as laser-processed printing plates eliminate the need for traditional film, reducing setup complexity and expenses. With hundreds of pad shapes readily available off the shelf, customers can often find a solution that meets their needs without the added cost of custom pads. This efficiency in setup and materials makes pad printing an attractive choice for businesses of all sizes.
Screen Printing
Screen printing involves a more complex setup process, including preparing the screens, stencils, and any required tooling for specific substrates. While initial setup costs can be higher, the method becomes highly cost-effective for large production runs, especially when using automatic UV screen printing equipment. The durability and vibrancy of screen printing make it a worthwhile investment for applications requiring bold, long-lasting prints.
6. Durability and Aesthetics
Pad Printing
Pad printing is ideal for fine details and sharp designs. It excels in achieving precise prints but may not offer the same vibrancy as screen printing.
Screen Printing
Screen printing provides bold and durable designs, making it ideal for both indoor and outdoor applications or items subject to wear and tear. For a detailed comparison of durability between screen printing and other methods, visit Deco Tech Group’s screen printing services page.
Conclusion
Choosing between pad printing and screen printing depends on the specific needs of your project. Pad printing is perfect for intricate, multi-dimensional printing, while screen printing shines in bold, large-scale, and flat-surface designs. To ensure optimal results and cost-efficiency, work with experts who understand your industry’s requirements. Learn more about selecting the right printing method at Deco Tech Group.