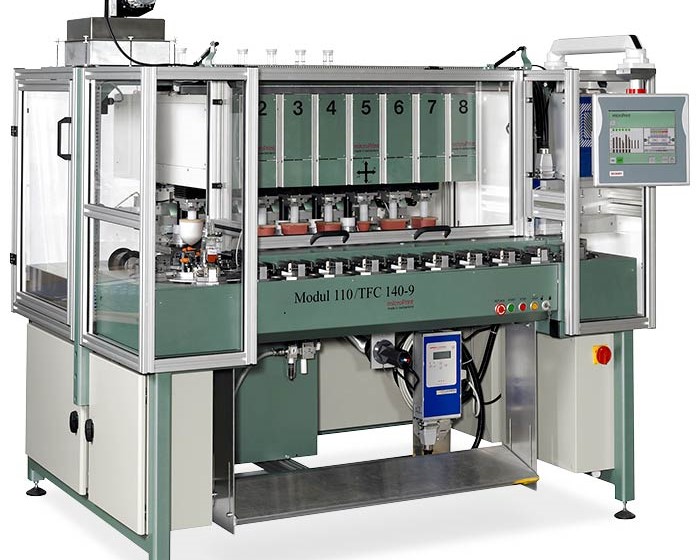
Advanced Techniques in Pad Printing: Maximizing Print Quality and Efficiency
Explore the Advanced Techniques of the Growing Billion Dollar Pad Printing Industry
In the world of industrial printing, where precision and efficiency are paramount, pad printing stands out as a versatile and reliable method for transferring images onto a variety of surfaces. With its ability to reproduce intricate designs with exceptional detail, pad printing has become indispensable across industries ranging from automotive to medical devices. However, to truly unlock its potential, manufacturers must harness advanced techniques that push the boundaries of print quality and efficiency.
Introduction:
Pad printing, also known as tampography, has undergone significant advancements in recent years, driven by innovations in materials, equipment, and process optimization. In this article, we delve into the realm of advanced pad printing techniques, exploring strategies to maximize print quality while streamlining production processes.
Enhancing Print Quality:
One of the primary goals of any printing process is to achieve impeccable print quality that meets the highest standards of clarity, color accuracy, and durability. Advanced pad printing techniques focus on several key areas to enhance print quality:
- Ink Formulations: Utilizing specialized ink formulations tailored to specific substrates and printing conditions can significantly improve print resolution, adhesion, and chemical resistance. Advanced ink formulations may include UV-curable, solvent-based, and silicone inks designed to achieve vibrant colors and long-lasting results.
- Image Preparation: Employing advanced image preparation techniques, such as high-resolution digital imaging (using software such as Abode Illustrator and Photoshop) and precise artwork adjustments, ensures optimal transfer of designs onto printing plates. Sophisticated image processing software enables fine-tuning of design elements to minimize distortion and maximize clarity during the printing process.
- Printing Plate Technology: Advancements in printing plate materials, such as polymer photopolymer plates and laser-engraved steel, laser polymer & anodized aluminum plates, offer superior durability and image reproduction capabilities. These plates exhibit excellent dimensional stability and precise etching, resulting in consistently high-quality prints over extended production runs.
Improving Efficiency:
In addition to print quality, maximizing efficiency is crucial for meeting production demands and minimizing operational costs. Advanced techniques focus on optimizing various aspects of the pad printing process to streamline workflow and reduce downtime:
- Automated Setup and Changeover: Integration of automated setup part handling and automatic feeding systems and quick-change tooling enables rapid adjustment of printing parameters and seamless transition between print jobs. Automated pad printing systems minimize manual intervention, reducing setup time and increasing overall productivity.
- Process Monitoring and Control: Implementing advanced process monitoring technologies, such as inline vision systems and real-time print quality inspection, ensures consistent output and early detection of defects. Closed-loop control systems adjust printing parameters dynamically to maintain optimal print quality throughout production runs.
- Lean Manufacturing Principles: Applying lean manufacturing principles, such as 5S methodology and value stream mapping, optimizes workflow efficiency and eliminates waste in the production process. Streamlined workflows and standardized operating procedures maximize throughput while minimizing resource consumption.
Conclusion:
In conclusion, advanced techniques in pad printing offer a pathway to achieve superior print quality and operational efficiency in industrial printing applications. By leveraging innovations in ink technology, image preparation, printing plate technology, and process optimization, manufacturers can elevate their pad printing capabilities to new heights. Embracing these advancements not only enhances the visual impact of printed products but also drives cost savings and competitive advantage in today's dynamic marketplace.